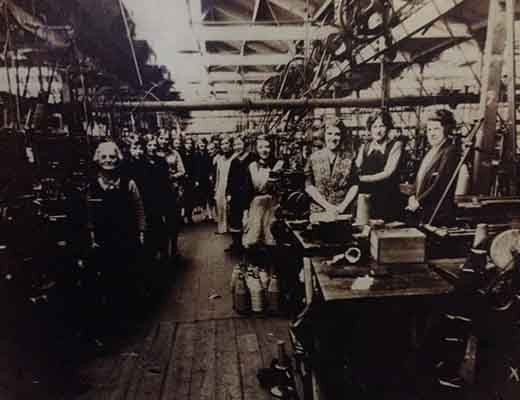
Spotlight on British Manufacturing – William Lockie and Company
29 May 2021The knitwear stocked by Humes Outfitters is expertly knitted a mere 20 miles away in the Border town of Hawick. William Lockie is steeped in history and tradition and although manufacturers, as a business, has many things in common with Humes. Both are family owned and run, and share many of the same core values with vast product knowledge, flexible service, highest quality standards and a commitment to their community, this is perhaps why the relationship between the two has grown from strength to strength.
Tip: See our full collection of William Lockie...
A long-standing history
Born in 1835, William Lockie was one of many who entered the hosiery trade in the late 1860s. The factory began production in 1874 in the Fore Row on the banks of the River Teviot, now Drumlanrig Square, where it remains today. With a keen business capability, attention to detail and supportive community spirit William Lockie found a ready market for the goods produced and the businesses began to flourish. Although married, Lockie had no family and the business was passed to his nephew Walter Thorburn, with the Thorburn family continuing to own the business today. It is the longest family owned and run British knitwear manufacturers still in existence and continues to play a pivotal role in the heart of the knitwear industry in Hawick.Weathering the Storm
Once there were as many as 250 woollen mills in Scotland, with the vast majority choosing to locate in Hawick. During the 1980s and 1990s British manufacturing changed significantly. Cheaper, offshore versions flooded the market causing many knitwear companies to cut corners in their production or fold completely. Ultimately this led to mass unemployment in towns like Hawick, who had once thrived off the textile industry, with less than ten factories producing out of the town today. Lockies remained true to their high standards and resisted against any temptation to compromise on their quality product, still embracing the truly unique manufacturing processes that have been successful for hundreds of years.How William Lockie Look After the Countryside
William Lockie has been creating premium knitwear since 1874, combining the very latest in knitting technology with traditional craftsmanship for a superior product that is hard to beat. They use all-natural fibres and there is no chemicals or harmful substances in their dyes. They wind back sweaters back into yarn to reknit them if they are unused and no chemicals are used in the washing process, just soft Scottish water from the local rivers which is recycled and reused.
Tip: Learn more about some of our sustainable brands...
A Precision Manufacturing Process
Knitting – William Lockie plain knit garments (Leven, Rob, Gordon and Oxton) are all knitted on traditional knitting frames. These machines have been used since the early 1920s and the quality of knit cannot be replicated by any other machine. In 1991 William Lockie embraced the newest technology with the introduction of the Shima Seiki machines. These advanced machines knit intarsias, intricate designs and textures which previously would have to be done by hand and although knitted on these new advanced machines, the garment still proceeds through the traditional handcrafted processes. The resulting blend provides a manufacturing capability which produces the most complex designs without compromising that unique Scottish quality and identity, providing you with a garment that cannot be duplicated anywhere else. Both knitting machines knit 4 singular panels; a front, a back and 2 sleeves along with any trims for cardigans, necks, cuffs, skirts and pockets.Did you know: At William Lockie they use more yarn than other manufacturers and knit at a tight tension to ensure an end product that is denser, smoother and holds its shape.
Initial Handcrafting - once knitted, the garment goes through 30 processes which include both machine and handwork. The 4 panels are linked on a binding machine, which closely matches up the stitches on each panel and strongly links them together using more yarn. They are then swift seamed up the sides of the body and the underarms, followed by bar tacking where the more vulnerable places (e.g. the underarm and cuff) are given an extra stitch by machine for extra reinforcement. Each of these steps is operated by one person per machine.
Washing – A significant part of the process, where the garment along with its yet to be added trims are washed together in the soft Scottish water from the local river which runs behind the factory. It is a vital step where the softness, size and wearability of the sweater can be easily compromised if done incorrectly.
Final Details – Once washed, the garment is paris pressed, it is pulled to its accurate size and blasted with steam, this ensures no sizing issues and allows the garment to bounce back to shape after the washing process. The neckline is then cut, and the collar linked on in a similar fashion to the body linking using binding machines. Cardigans, zips and pockets are stitched on with buttons and buttonholes added to the required styles and some final hand sewing takes place to tidy up the loose ends.
Quality Check and check and check – unlike other manufacturers who spot check items, every single William Lockie garment is checked for quality before leaving the factory. In fact, the intricate designs knitted on the shima machines are also inspected after they have been knitted, before being linked together, quickly identifying any knitting issues. Once they have been labelled and given a final press each garment is checked over again before being packaged up to be dispatched.
Sourcing the best raw materials – Fibres Explained
Cashmere – unparalleled in luxury, warmth and softness, cashmere comes from the Hircus Laniger goat in the freezing climates of Inner Mongolia. The undercoat of the mountain goat is painstakingly combed by nomadic tribesmen from thousands of ultra-fine fibres hiding under their longer, coarser outer coat. This soft undercoat allows them to survive the most hostile environments with freezing winters of -40 °C. Once the fleece has been combed it is divided by colour and fineness with all subpar fibres discarded, this ensures consistency and the highest quality, grade A cashmere available. The fleece is then dyed and spun into yarn by world renowned British spinners. Working closely with the dehairers and farmers in Mongolia, the spinners have full traceability of where the cashmere has come from, ensuring the welfare of the animals is a top priority along with sustainability and preserving the environment and eco-system from which they graze.
Lambswool – also known as “Geelong Lambswool” comes from specially bred Australian sheep. Reared in the Geelong region where the climate is mild, producing a softer finish. Due to the cold and damp climate in Britain, most of the wool here is used for carpets. Like Cashmere, the wool is shipped to the UK where it is dyed and woollen spun by British Spinners.
Did you know: William Lockie source 100% pure fibres for their knitwear and only the best makes the cut.
Super Geelong – also known in the industry as “virgin wool” is the first clip of Geelong lambswool. As with most baby animals, the lambs first coat is softer than when they reach adulthood. It is made up of finer micron fibres which means not only is it slightly softer than lambswool it can also be knitted in a lighter weight.
Camelhair - Coming from the specially bred “Two Humped Bactrian Camel,” which lives and roams in the Gobi Desert, it is 100% natural and undyed which is why it is available in only one colour.
Did you know: William Lockie cashmere, lambswool, super geelong and camelhair are all spun and dyed from wool in the UK by Scottish Spinner Todd & Duncan in Kinross and English spinner Hinchcliffe & Sons in Yorkshire.Merino – also sourced from the same Australian sheep the difference with merino wool is all in the spinning of the yarn. Worsted spun by the premium Italian spinners it is an active fibre that reacts to changes in body temperature, keeping you warm or cool and absorbing moisture making it a comfortable and breathable fibre.
Did you know: Worsted spun yarn is combed in a way that all the fibres of the fleece are going in the same direction resulting in a smooth and silky like result, unlike woollen spun where the fibres are going in all directions giving woollen spun knitwear that classic “hairier” look.
Finding the right William Lockie garment
With different fibres, plys and shapes it can be difficult to find the right William Lockie piece for your wardrobe.
Ply – refers to the weight of the garment. For example, the William Lockie Oxton and Gordon collections are 1ply cashmere and super geelong respectively. 1ply is where one thread of yarn is used, this is the lightest weight of knitwear that we offer. The Melrose, Leven and Rob collections are 2ply, and are thicker garments than the 1ply as two threads of yarn are twisted together to be knitted, and so on.
Sizing – knitwear sizing is accurate to measurement and surprisingly to some, is not the same as jacket sizing. It is simply the measurement across the chest from directly under the armhole to the other armhole, in inches and doubled. For example, a William Lockie size 44” will measure roughly 22” across the chest from armhole to armhole. At A Hume, we recommend finding your best fitting sweater, laying it out flat and measuring it this way.
Shoulder Shapes – William Lockie classic sweaters come in two shoulder shapes, the saddle shoulder and the set-in sleeve. The saddle shoulder, a style feature of models such as the Leven and Melrose are more generous across the armhole providing a more classic fit. The set-in sleeve styles such as the Oxton, Gordon and Rob are more fitted.
The Future of British Manufacturing
William Lockie are no strangers to navigating through uncertain times. They have survived two World Wars, recessions and an influx of offshore manufacturing. They are hopeful that the future sees a bigger emphasis on the importance of British Manufacturing, providing security for their 125 local workers and supplying the market with a true quality, Scottish product.